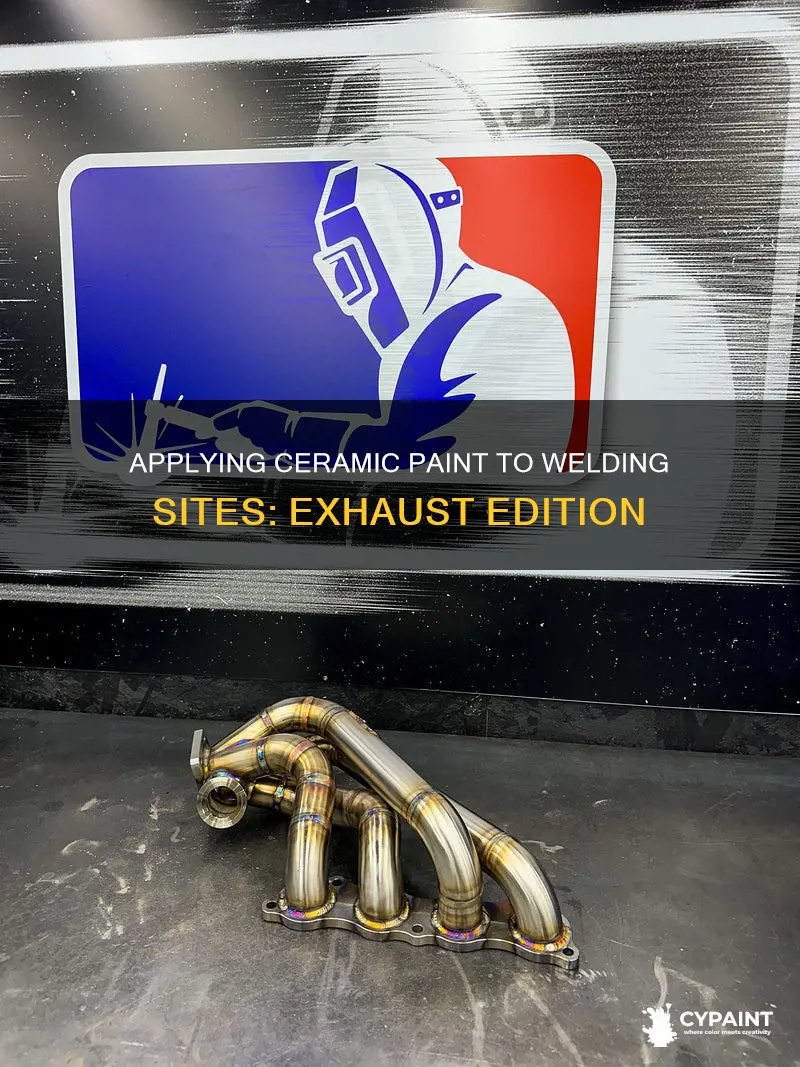
Exhaust ceramic coatings are a popular way to enhance performance and heat management in cars and bikes. They are also a great way to finish welding sites. To ensure the best results, it is important to follow some key steps. These include wearing gloves during installation to prevent contaminants, cleaning the surface with hot soapy water, and avoiding harsh impacts. In terms of the paint application process, it is recommended to use a spray gun and start with hard-to-reach areas, making big sweeping passes to ensure complete coverage. After application, the paint should be left to dry and then cured in an oven at specific temperatures.
Characteristics | Values |
---|---|
Type of paint | Ceramic paint |
Paint temperature resistance | Up to 2000 F |
Paint brand | Powder by the Pound |
Paint colour | Black satin |
Paint application method | HVLP spray gun |
Paint curing temperature | 450 F |
Paint curing time | 1 hour |
Paint curing method | Oven |
Additional paint application | Refrain from applying additional paint over ceramic coating |
Paint maintenance | Minimal, clean with hot soapy water |
What You'll Learn
Preparing the exhaust surface
Firstly, it is essential to clean the exhaust surface thoroughly. Any remaining oil, grease, or dirt on the surface can hinder the adhesion of the ceramic paint. Use mineral spirits or a suitable wax remover to ensure the surface is free of any contaminants. This step is vital to ensure the paint adheres properly and does not peel or flake off prematurely.
The next step is to roughen the exhaust surface. This process can be achieved through sandblasting or using a vapour blaster. Roughening the surface creates a profile that enhances the paint's adhesion. It is important to note that while sandblasting is effective, it may not be necessary for all projects. For smaller or intricate areas, manual sanding or wire brushing can be employed to create the desired surface profile.
In some cases, it may be advisable to apply a primer before painting. A weld-through primer, such as zinc weld-through primer, can provide excellent rust resistance and mimic the coating found on vintage BMW exhausts. Additionally, cold galvanizing paint can be used, but it tends to smoke initially and may not be ideal for areas closer to the engine.
Before painting, it is crucial to ensure the exhaust surface is dry and free of any moisture. This step is especially important if the exhaust has been washed or exposed to rain. Allowing the surface to air dry or using compressed air to accelerate drying can help achieve the desired results.
Lastly, consider the environment and temperature when preparing the exhaust surface. Working in a well-ventilated area or outdoors is recommended when dealing with paints and solvents. Additionally, maintaining a consistent temperature that aligns with the paint manufacturer's recommendations can impact the paint's performance and curing process.
By following these steps and considerations, you can effectively prepare the exhaust surface for ceramic paint application, ensuring a durable and aesthetically pleasing finish.
Authenticating Art: How to Spot a Fake Painting
You may want to see also
Choosing the right paint
When it comes to choosing the right paint to finish welding sites with ceramic paint on exhausts, there are several factors and options to consider. Firstly, it's important to understand that normal paint or powder coat are typically not suitable for this specific application. Instead, you should opt for specialized paints designed for high-temperature environments, such as those generated by exhaust systems.
One popular option is to use a high-temperature engine paint. These paints are designed to withstand higher temperatures and can be a suitable choice for exhaust applications. However, it's worth noting that some users have reported varying levels of success with different brands and types of high-temperature engine paints. For example, VHT High-Temp Exhaust paint has been known to burn off pipes, while POR-15 High Temp paint has shown better adhesion.
Another important consideration is the application method. Some paints, like Mipatherm, are only available in tins and require a spray gun for application. On the other hand, aerosol paints offer convenience and ease of use but may not provide the desired coverage or longevity. It's crucial to follow the manufacturer's instructions for application and curing to ensure the best results.
Zinc-based paints, such as zinc weld-through primer and cold galvanizing paint, have also been used with some success. These paints can provide rust resistance and mimic the coating on vintage BMW exhausts. However, they may smoke initially and require a heavier application to ensure effectiveness.
Ultimately, ceramic coating has been praised for its durability and long-lasting performance. While it may be more expensive and require a more involved application process, it is known to withstand the test of time. When applying ceramic coating, it's essential to follow the recommended procedures, such as curing at specific temperatures and avoiding harsh physical impacts on the coated parts.
Where is Illustrator's Live Paint Bucket Tool?
You may want to see also
Applying the paint
When applying ceramic paint to an exhaust, there are several steps to follow to ensure a long-lasting and effective finish. Firstly, it is important to prepare the surface by cleaning it with a suitable product, such as wax remover or mineral spirits, to ensure complete removal of any contaminants, such as oil or dirt. This is crucial as contaminants can compromise the performance of the coating. A user on the MIG Welding Forum recommends roughening up the surface a bit, in addition to cleaning it.
Once the surface is prepared, the next step is to apply the paint. It is recommended to use a spray gun for this purpose, as aerosol sprays often provide uneven coverage and may not last long. When spraying, start with the hard-to-reach areas and then move on to big sweeping passes. Ensure complete coverage by inspecting the pieces carefully.
After application, let the paint dry for at least 30 minutes. The curing process then begins, which involves placing the parts in an oven and heating them to a specific temperature for a set duration. For example, one type of VHT paint requires curing at 450°F for one hour, followed by a final cure at 750°F or higher for at least one hour. It is important not to place the parts in a preheated oven, as this can cause solvent pop.
Finally, reassemble and install the cured parts. It is recommended to wear gloves during this process to prevent any oils or dirt from transferring onto the coating. Once installed, take the vehicle for a drive and get it up to operating temperature for at least one hour to complete the curing process.
Erase Paint Lines Without Affecting Images: A Simple Guide
You may want to see also
Curing the paint
To ensure a successful curing process, it is essential to follow the manufacturer's recommended curing times and application instructions. Rushing the curing process can compromise the effectiveness of the coating, leading to suboptimal performance in protecting your vehicle's paintwork. The curing time can vary depending on several factors, including the type of coating, environmental conditions, and application thickness. A thicker application will generally require more time to cure compared to a thinner layer.
To optimize the curing process, it is advisable to apply the ceramic coating in a controlled environment, such as a garage, to minimize the impact of external elements and temperature fluctuations. High temperatures accelerate the curing process, while cool temperatures slow it down. Proper ventilation in the application area is also important.
During the curing period, it is crucial to avoid exposing the coated surface to water or moisture. Minimizing handling or contact with the coated surface is essential to prevent disruptions in the delicate curing process. Following specific post-application guidelines provided by the manufacturer will ensure a durable and effective cure.
Some ceramic coatings may require several days to a few weeks to achieve a full cure, and in some cases, peak performance may be reached after a month or longer. It is worth noting that high-quality products from trusted brands can also make a significant difference in the curing process and the overall protection provided by the ceramic coating.
Exporting Substance Painter Materials to Unity: A Step-by-Step Guide
You may want to see also
Maintaining the ceramic coating
Preparation is Key: Before applying any ceramic coating, ensure that the exhaust surface is properly prepared. Clean the exhaust tubing with a suitable solvent, such as mineral spirits or wax remover, to eliminate any residual oil or grease. This step is crucial for the coating to adhere correctly.
Choose the Right Product: Opt for a high-temperature ceramic coating designed specifically for exhaust systems. These coatings are formulated to withstand extreme temperatures generated by internal combustion engines. Additionally, consider the application method, as coatings are available in spray, oven-baked, or air-cured formulas.
Avoid Additional Paint: Do not apply additional paint over the ceramic coating. Using standard paint that is not designed for high temperatures can cause deformation and ruin the aesthetics of the original ceramic finish. If you wish to change the appearance, consider using a coloured ceramic coating or a suitable wrap.
Prevent Moisture Trapping: Avoid wrapping a ceramic-coated exhaust, especially with materials like exhaust wraps. Wrapping can trap moisture underneath, especially in humid conditions or when exposed to rain. This trapped moisture can lead to rust corrosion, compromising the performance and integrity of the coating and the exhaust system itself.
Regular Cleaning: Regularly clean your ceramic-coated exhaust to maintain its appearance and performance. Use mild detergents and soft cloths to prevent scratching or damaging the coating. Ensure the exhaust is thoroughly dried after cleaning to prevent water spots and potential moisture issues.
Handle with Care: While ceramic coatings are known for their durability, it's important to avoid harsh impacts or abrasion. Treat your coated exhaust with care during installation, maintenance, and transportation to prevent chipping or scratching the coating.
By following these maintenance guidelines, you can maximize the lifespan, performance, and aesthetic appeal of your ceramic-coated exhaust system.
Exporting ZBrush Skin Paint to Substance: A Step-by-Step Guide
You may want to see also
Frequently asked questions
Mipatherm is a good option, but it's only available in a tin and you'll need a spray gun.
You could try a tin of Autotek AT0VHTB500 500ml VHT Paint - Black ASIN: B004ZJIP86. This has good coverage and is long-lasting, but it requires baking at 400 degrees Fahrenheit for an hour and then slowly increasing to the maximum operating temperature.
You could try a cheap-o Harbor Freight HVLP spray gun and black satin ceramic header paint. This will cure at 450 degrees Fahrenheit for an hour and then needs to be taken for a drive to get the vehicle up to operating temperature for at least 1 hour.
Normal paint or powder coat is not suitable for this use.
Yes, it is recommended to wear gloves during the installation process to prevent any oils and dirt from transferring onto the coating.